Special Machines. Automation and Robotization
We offer comprehensive services in the design, manufacturing, and implementation of special machines, encompassing automation and robotics. Thanks to the experience of our engineering and technical team, we embrace challenges and analyze each project with due diligence to meet customer expectations. The solutions we propose consider not only technical and functional requirements but also durability, reliability, production and operational costs, and the potential for future expansion. Using advanced CAD software, we prepare complete technical and production documentation, as well as graphic visualizations when needed. We are confident that the machines designed and manufactured by Stomet meet the highest standards in terms of functionality and safety.
We specialize in manufacturing machines and devices related to rubber and plastic processing, including:
- Roughening and cleaning stations
- Cutting and notching machines operating in-line or independently
- Fixed or interchangeable cutting and/or notching modules
- Eccentric drills
- Profile winders (winding on spools or trays)
- Roller and discharge conveyors
- Cooling baths
- Mixture feeders
- Cord/tape/profile compensators
- Drives for bending cassettes
- Manipulators and loading/unloading plates
- Loading plates with presence detection of dedicated inserts
- Cutting knives (straight and shaped)
- Control templates
We understand that today’s production stations are expected to provide not only high quality and reliability but also maximum safety and autonomy. At Stomet, we comprehensively realize robotic and automated production stations according to customer requirements:
- Automated stations for loading components into injection molds
- Automatic and semi-automatic assembly stations
- Automated cutting and grinding (using robots)
We offer automation and robotics for existing production processes, as well as the reconstruction and modernization of used machines. We have successfully completed many projects that have helped our clients increase process efficiency and reduce production costs. The experience we have gained over the years in various industrial sectors allows us to understand our clients' needs perfectly, which is crucial for selecting optimal solutions. Our services include:
- Automation and robotization of production processes
- Modernization or modification of used machines
- Adapting machines to minimal/essential requirements
We collaborate with leading robot suppliers, including ABB, Kuka, and Mitsubishi, and we are ready to implement applications using robots according to customer preferences.
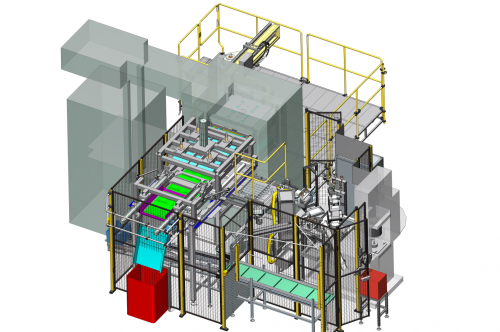
Line for the production of a rubber-metal connector for car suspension
Operations: Production of a rubber-metal product by injection moulding, calibration of the product, 100% visual inspection and packaging.
Main elements:
- Manipulator with loading plate for metal parts
- Product unloading station and injection channel
- Product receiving feeder system
- Robot with equipment installed
- Control systems for flash, product diameter, short shots, marking and OK/NOK segregation
- Packaging and transport of packaging
A line designed to work with an injection moulding machine and a hydraulic press.
Overall dimensions of the stand L x W x H: 7100 x 7250 x 3000
Operations: The loading of the metal parts is followed by injection and vulcanisation of the rubber mix. Once the mould is opened, the injection and overflow channels are automatically removed and the vulcanised rubber-metal products are discharged. Using a conveyor, the products are moved to the calibration and marking station. After visual inspection, the products are packaged and transported to the collection point.
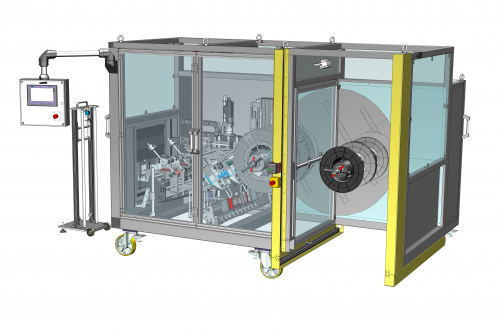
Rubber profile winding machine.
Operations: Winding of rubber profiles on cardboard / plastic spools.
The overall dimensions of the supported profiles L x W: 3-80 x 3-60 mm.
Supported profile length: 10 - 1000 m.
Maximum winding speed: 50 m/min.
Maximum speed of the cooperating extrusion line: 40 m/min.
Options:
- simultaneous winding of identical profiles on two spools,
- interchangeable cores for plastic or cardboard spools.
- cutting system - a machine equipped with a measuring system to ensure the correct length of cut. Preliminary cutting and final cutting after reaching a user-set length.
- Conveyors and reel speed control systems enable tracking work, i.e., automatic adjustment to work with the extrusion line.
- laying section suitable for interchangeable dedicated mouthpieces.
Overall dimensions L x W x H: 2800 x 1900 x 2000
Operations: after winding the preset length, winding is automatically stopped, profiles are cut off, and the turntable moves to move the wound spools to the unloading zone and empty spools to the winding zone at the same time. When changing spools behind the safety barrier, the re-winding starts, allowing continuous operation without unnecessary stops.
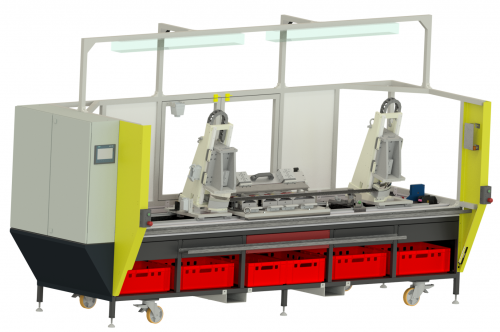
Machine for cutting and punching the rubber profile
Operations: cutting to a given length and performing shape cuts,
Overall dimensions L x W x H: 3900x1420x2300
The machine can optionally be equipped with interchangeable modules, configurable depending on the requirements of a given product.
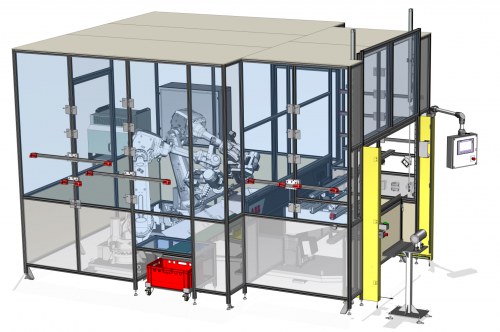
Universal cutting machine
Operations: Cutting and grinding of rubber profiles with aluminium insert
Supported profile length: 300 - 1500 mm.
Options:
- machine equipped with two robots with a complete cutting and grinding system installed and a positioner (rotary table) with two assembly stations,
- tooling detection and correctness checking system,
- detecting the correctness of the product assembly in the tooling,
- automatic extraction system for cutting and grinding + additional cleaning station after cutting and grinding.
Overall dimensions L x W x H: 3500 x 4700 x 3365
Operations: the machine, thanks to the use of a rotary table, allows simultaneous machining of the workpiece and assembly of the next product to be machined. This ensures that work is carried out continuously without unnecessary downtime.
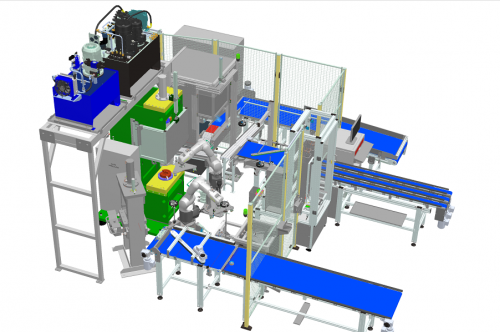
TOP-MOUNT product assembly and rolling line
Operations: Assembly and rolling line for rubber and metal products
Main elements:
- two hydraulic presses with tooling set
- in-line feeder system
- two robots with installed gripper sets
- tooling detection and correctness checking system,
- vision system for detecting and checking the correctness of components and finished products,
- a system for detecting the correct installation of the product in the tooling,
- laser marking of finished products
Overall dimensions L x W x H: 6300 x 5850 x 3700
Operations: The main components of the line are two hydraulic presses, in which the assembly and rolling operations of the components are carried out. The components placed on linear feeders, after being inspected by the vision system, are picked up and positioned by robots. The robots then place them in the tooling of the presses where the assembly process is performed. Once the assembly, inspection and labelling process is complete, the products are deposited on a transfer feeder. Incorrect components and incorrect finished products are rejected to the separators.
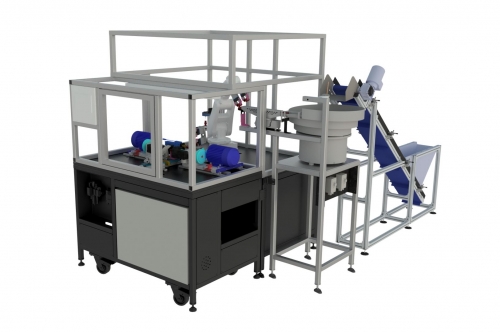
Robotization of the product chamfering station
Operations : sleeve transport, length control, chamfering, chamfer and bore control, good/ bad part segregation.
Dimensions L x W x H : 2050 x 3620 x 2050
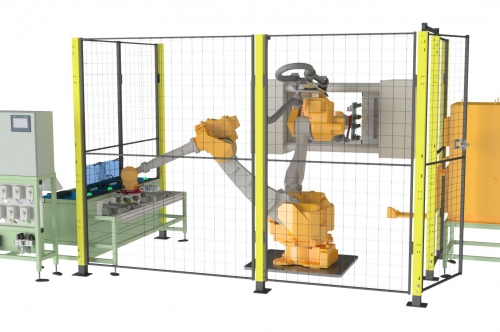
Automation for the loading of sleeves into injection moulds
Operations : the robot equipped with a loading gripper takes the sleeves from the automatic vibrating feeder and places them into the dedicated injection mould.
Dimensions L x W x H : 5000 x 2200 x 2300
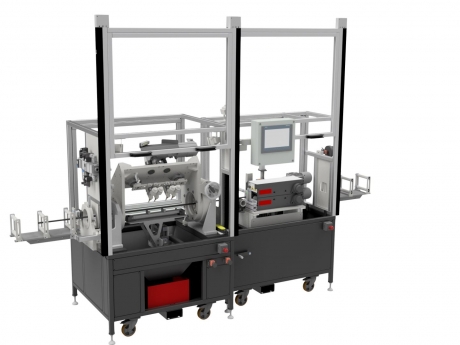
Rubber profiles drilling machine with tracking system
Operations: track controlled drilling of rubber profiles within technological line
Line speed range: 0-30 m/min.
Line synchronization: by means of marker, encoder or programmed sections.
Hole intervals: 55 -1 000 000 mm
No. of drilling units: 1 – 4 (software controlled).
Options:
- drilling units positions can be set on bar with range 500mm,
- holes can be drilled at fixed angle with adjustment range +/- 45° (from vertical plane),
- possibility of extension by next „slave” unit controlled from main module.
Dimensions L x W x H: 3680 x1160 x 2740
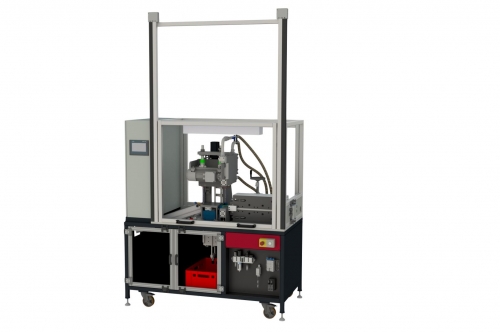
Machine for cutting and punching
The machine is dedicated to automatic cutting into a given length and cutting a rectangular "window" in the rubber profile.
Dimensions L x W x H : 1700 x 840 x 3000
Operations : the machine cuts with a circular saw into the desired length and cuts the "window" in the profile.
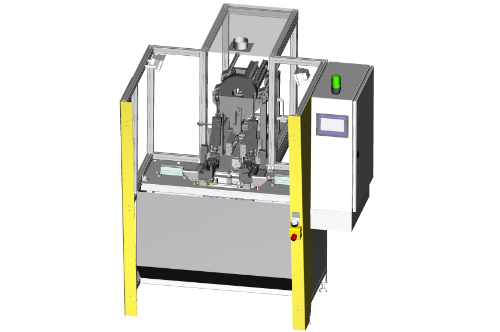
Machine for joining of rubber profiles
Machine for precise and repeatable joining of rubber seal ends using plastic film. The machine is equipped with an automatic joining and film feeding system. Interchangeable tooling allows adaptation to the cross-section of the seal.
Operating Principle:
The machine enables the joining of rubber seal ends using plastic tape. The seals are placed into dedicated slots according to the profile cross-section. To ensure the correct position, the profiles are pressed using a pneumatic clamp. The plastic tape is fed between the profiles. The tape and seal ends are heated using infrared emitters, after which the welded ends are pressed together. Once welding is complete, the tape is automatically cut, and the pressure is released.
Main Technological Features:
- Precise and repeatable welding of seal ends using plastic film
- Maximum cross-section of the joint: 40x40 mm
- Interchangeable tooling depending on the cross-section of the seal being welded
- Heating system for seal ends and plastic film using radiators
- Automatic welding system, including: pneumatic sealing clamp, film feeding, heating, pressing of welded ends, cutting the film, and releasing the clamps
Dimensions: L x W x H: 1750 x 1550 x 1650
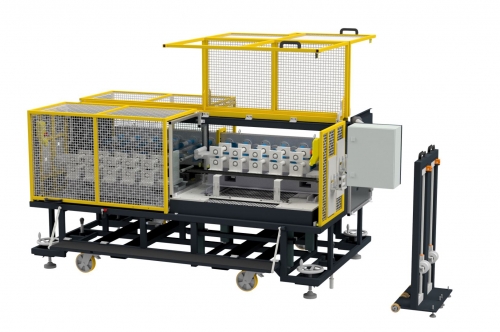
Drive for the roller bending cassettes
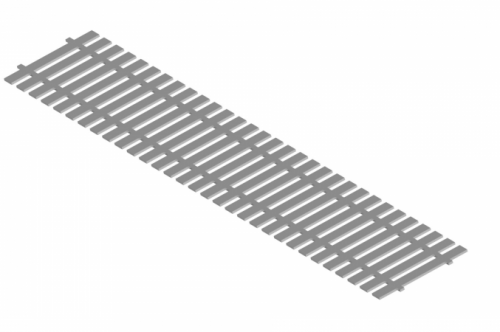
The machine is designed to drive dedicated bending cassettes.
Dimensions L x W x H : 3215 x 1800 x 1580
Operations : the machine is equipped with two drive cassettes (each with 6 stations). The regulation of the cassette position enables simultaneous work on 2 production lines.
It is allowed to install one long cassette with 12 stations in one production line.